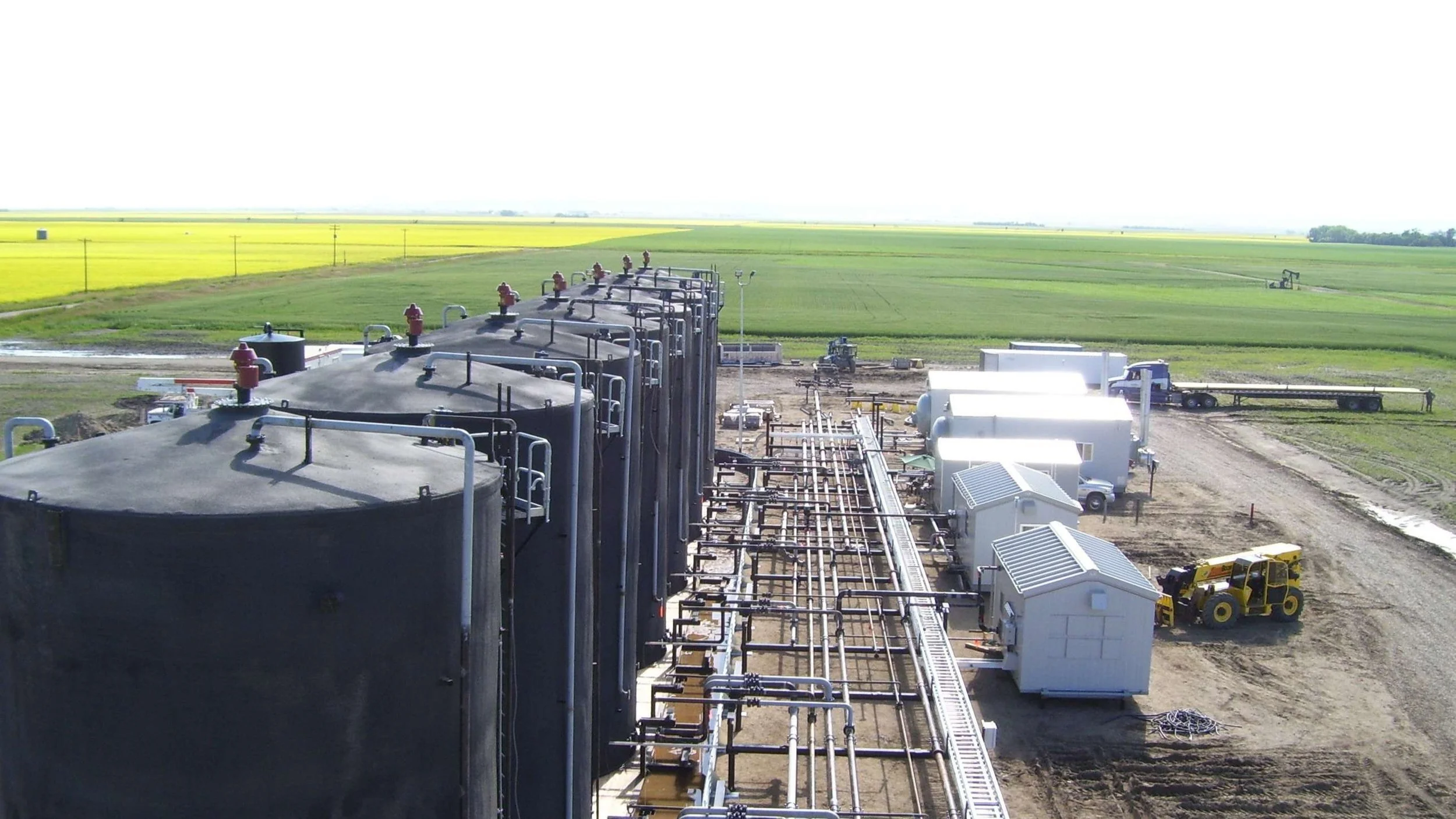
Oil Facilities
Capabilities
Sour and sweet oil batteries
Separation & coalescing
Treating (BS&B / H20 content)
Desand & desalt systems
LACT stations
Tank terminals
Recycle & tankage & shipping
Truck loading & off-loading
Well tie-ins & multi-well pads
Produced water injection & treating
Flare & incineration
Regulatory compliance
Previous Projects
-
Multi-well Oil Battery - 250 m3/d
This project involved completing the engineering and design of a multi-well oil battery near Grande Prairie, Alberta.
The battery improved production, operability, and run times of the existing wells by reducing field operating pressure and mitigating wax and hydrate formation.
Project details:
The facility was designed for 113E3 m3/d of gas and 250 m3/d of oil
3 x 2,000 bbl sales tanks
2 x 750 bbl water / emulsion tanks
Other elements included: inlet separator, fired heater, solution gas compressor, flare stack, LACT Unit, MCC, Genset, and office building designs.
-
Oil Treating Facility - 3,000 bbl/d
Lanmark was engaged to engineer and design updates to increase the capacity of an existing battery to 3,000 bbl of oil, 7,000 bbl of water, and 6.5MM scf/d of sour gas (4% H2S, 4.5% CO2).
Project details:
750 bbl oil storage tank
750 bbl water storage tank
Vapour recovery unit
1,100 HP sales compressor
Other elements included: 6’ x 24’ Inlet slug catcher, new 60’ flare stack, and 800 kW generator.
-
Oil Battery - 10,000 bbl/d
This project was for the design, procurement, and construction of an oil battery facility to receive oil emulsion via pipelines and trucks for separation of gas, oil, and water.
Project details:
2 x 950,000 BTU/hr heated oil treaters
Lease Automatic Custody Transfer (LACT) package including oil shipping pump
7 x 2,000 bbl tank farm (oil effluent storage, sales oil, and produced water storage)
Lanmark identified gas plant system capacities and made recommendations for the optimization of the amine system which resulted in savings of approximately $1 MM annually.